Choosing The Right Screw For Your Metal Panels
Something as small and simple as screws and fasteners are easy to disregard as a vital component of a construction project. For metal roofs, fasteners make up less than 1% of the total cost of installation, yet they can result in 100% of the roof’s failure.
Your roof can fail from broken fasteners, incorrectly installed fasteners, worn out sealing washers, or the simplest of errors: using the wrong screws.
At Western States Metal Roofing, we manufacture metal roofing and metal siding panels for a wide variety of commercial and residential projects. We’ve worked with thousands of contractors over two decades and continuously receive questions on which type of screws to use.
The answer, of course, is not always so simple. There are many different factors you have to consider when choosing the right screw for your metal roofing or siding project.
In this article, we’re going to go over the different fasteners to help you decide which metal roofing fastener will work the best for your specific project.
Factors To Consider When Choosing A Metal Roofing Fastener
- Type Of Panel System
- Screw Colors
- Fastener Identification
- Screw Coating And Material
- Screw Length Needed
- Type Of Screw Needed
- Tek/Self Drilling Screws
- Screw Drill Points
- Screw Sizes
- Screw Head Types
- Thread Count
If you’re a DIY installer then you will need to know how to correctly fasten the metal roofing screws. We can help you with that also.
Choosing The Correct Fastener For Exposed And Concealed Panel Systems
The type of fastener you use depends on whether you are installing exposed fastener panels or concealed fastener panels. Wavy corrugated and R Panel are examples of exposed fastener panels. Standing seam or flush wall panels are a concealed fastener panel.
When installing exposed fastener panels, fasteners with rubber sealing washers are used to increase the weathertightness of the panels and keep water out.
Concealed fastener panels use fasteners with a low profile head to avoid contact with the underside of the roofing panel.
Concealed fastener panels that use clip attachments, such as snap lock standing seam, generally use pancake head style fasteners. A system that does not use clips, such as nail strip standing seam, uses extra low profile style fasteners.
Matching Screws To The Color Of Metal Panels
Metal panels come in a wide range of colors. Luckily, so do fasteners.
Screws are available with color-coated fastener heads to match the color of your metal panels. This makes the fasteners blend in with the metal roofing and siding panels for a more polished and neat appearance.
Fastener Identification
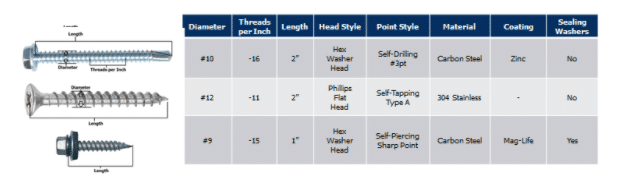
These are the main components to the anatomy of a fastener
- Diameter - The shank diameter and not the diameter of the screw head.
- Threads Per Inch - Example: A screw that’s a #12-14 is a #12 diameter with 14 threads per inch.
- Length - Starts from the underside of the head and includes the drill point & sealing washer. The head style is included in the length on countersunk fasteners only.
- Head Style - The most common metal roofing screws are hex head, hex washer head, and pancake head.
- Drill Point Style - Self-drilling, self-tapping, and self-piercing
- Material - Carbon steel and stainless steel are the two most common.
- Coating - Galvanized screws are the most common. The screw head is usually painted the same color as the metal panels.
- Sealing Washers - The screws will either have a rubber sealing washer for weather-tightness or will not.
Select The Right Screw Based On The Type Of Material
When selecting the material of your screws, consider the type of metals the screws are fastening into. When dissimilar metals are in contact and are exposed to moisture, galvanic action occurs.
Galvanic action between dissimilar metals can result in premature fastener failure that leaves your panels at risk for leaks to occur. Simply put, when certain metals come in contact with each other, one metal will sacrifice itself to the other.
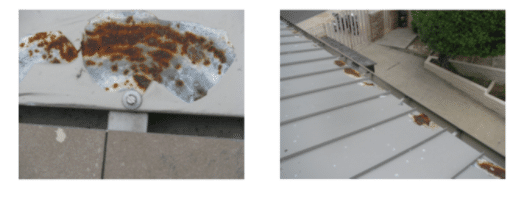
Generally, the further apart the materials are in the galvanic series (see the chart below), the higher the risk of galvanic corrosion. The farther apart the metals are on the chart, the greater the corrosion will be.
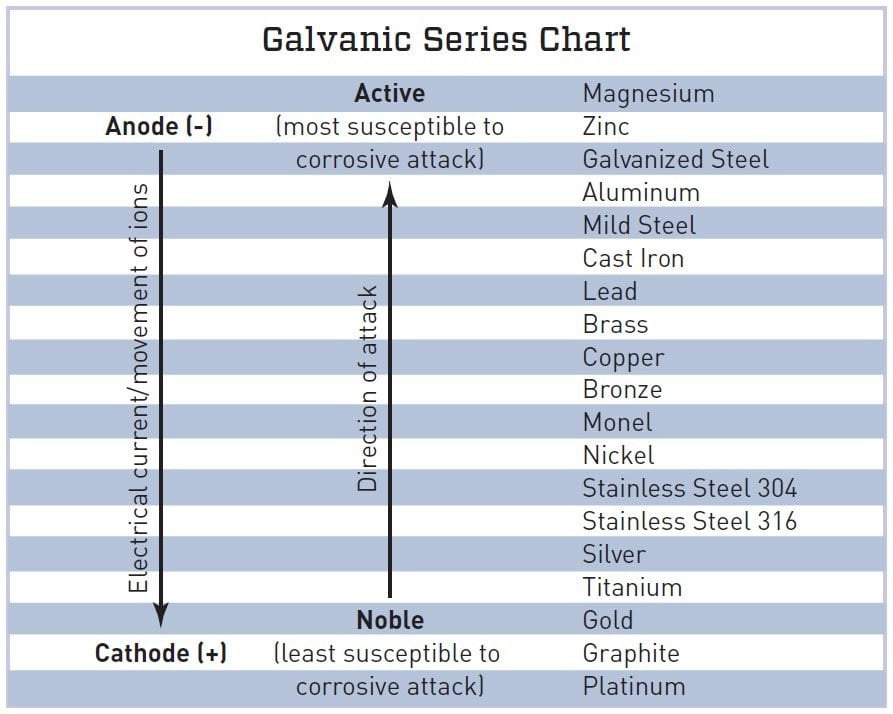
What Type Of Screw Coating To Use On A Metal Roof?
Your metal roofing and siding materials on your job will dictate the finish, coating, and materials for the appropriate screws.
- Aluminum Roofing - Use stainless steel type 304 screws with a matching paint color on the screws heads. Never use 410 stainless steel on an aluminum roof.
- Copper Roofing - Use stainless steel type 410 screws that are also copper-plated.
- Corten Roofing - Use stainless steel screws with a dark brown painted screw head.
- Metal Roofing - Use zinc plated screws, which will be referred to as galvanized screws. The screw heads should be painted the same color as your metal roofing or siding panels.
What’s The Correct Screw Length For Metal Roofing?
If your fasteners aren’t long enough to penetrate through all of your material, it’s safe to say you’re not going to have a successful installation. The right fasteners must not only be long enough to go through the material, but you must also take into account the length of the drill bit if you are using self-drilling screws.
Most importantly, you want at least one inch of screw penetration into the material that you are fastening to.
The length is usually rounded up to the next half or quarter inch to ensure the fasteners are long enough. Keep in mind that the longer the screw, the more torsional strain is produced during driving. Sometimes this can cause the fasteners to break during installation.
Screw Lengths For Metal Roofing
The length of the screw is measured differently depending on whether the screw is a hex head or a flat head. Hex head screws will be measured from the bottom of the hex head and flat head screws are measured from the top of the screw head.
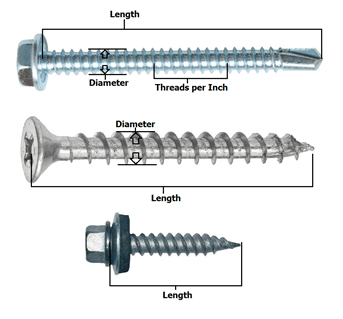
Different climates and load requirements mean that the screw length will not always be the same. Every job should be treated independently.
Here are some general guidelines:
- Standing Seam Metal Roofing - 1” pancake heads are the most typical screws to fasten the clips.
- ½” Corrugated - The screw will fasten to the high of the panel in a roofing application. This panel is ½” in height, so you will need at least a 1.5” long screw.
- ⅞” Corrugated - The screw will fasten to the high of the panel in a roofing application. The corrugated roofing is ⅞” in height, so you will need at least a 2” long screw.
- R Panel, 7.2 Panel, and Ag Panels - The screw will fasten to the low of the panel. Screws that are 1” in length are the most common.
Screw Lengths For Metal Siding
Just like a metal roof, the requirements of the job will always vary. Always check with your engineer. Here are some general guidelines:
- Concealed Fastener Wall Panels - 1” pancake heads are the most typical screws.
- Exposed Fastener Panels - The screw will fasten to the low of the panel. Screws that are 1” in length are the most common.
Types Of Screws For Metal Roofing
Choosing the correct type of metal roofing fastener depends upon what the fasteners will attach to during installation. Most residential roofs will have a plywood substrate. Commercial or agricultural jobs can also be attached to wood, but it’s also common to attach screws to light gauge metal purlins or heavy steel I-beams.
Pro Tip: Always order screws with sealing washers as shown below to prevent roof leaks.
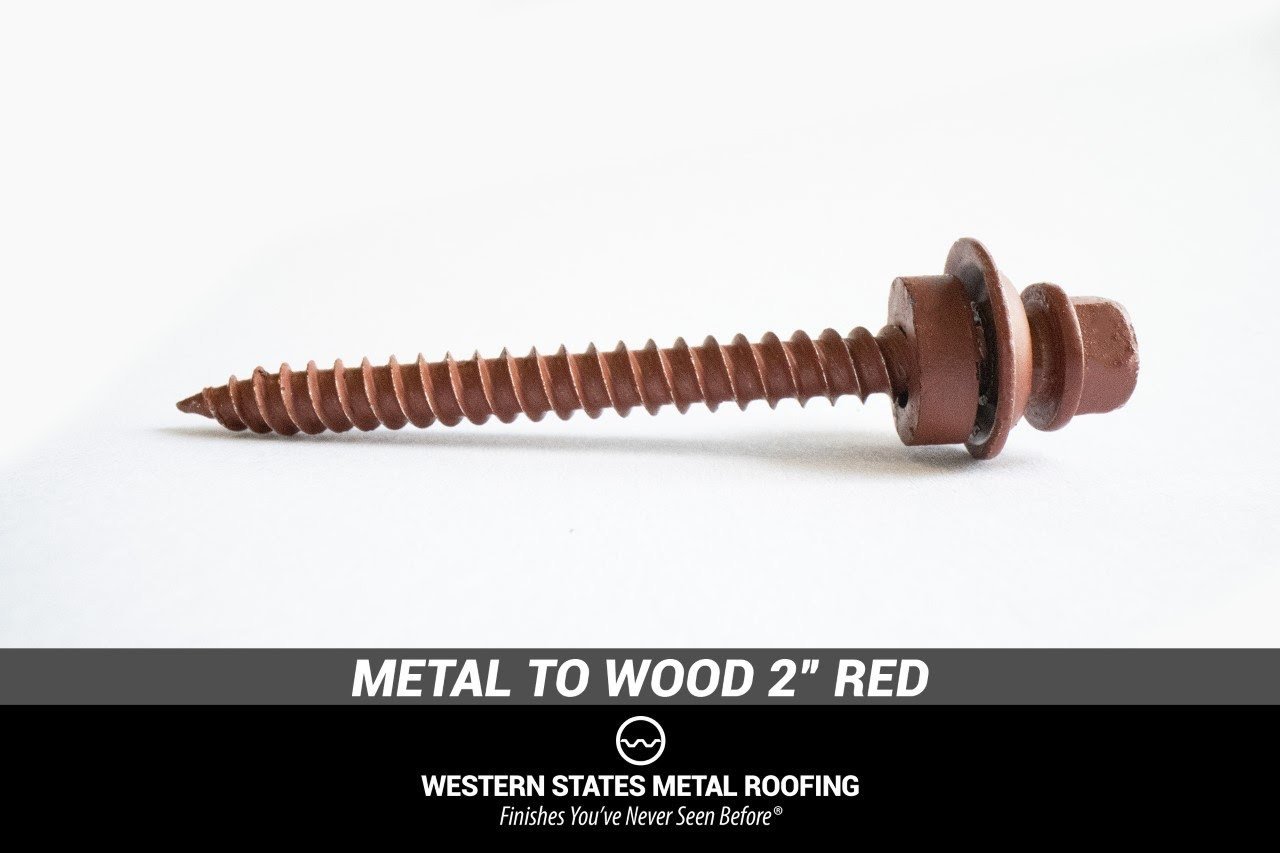
Roofing Screws Metal To Wood
The most common type of metal roofing fasteners are metal to wood roofing screws. Fastener manufacturers usually specify pull-out strengths for a variety of different types of wood as not all wood is the same. This helps to determine the right fastener for your project.
An example of a fastener for a wood substrate is the #9 metal to wood screw or the #10 metal to wood roofing screw. These screws have an extra sharp self-piercing point that can penetrate 20-29 gauge steel sheeting and then into the wood without pre-drilling, slipping, or damaging the metal panels.
Metal To Metal Roofing Screws
There is more than one type of screw that you can use when you attach to metal or steel. The right screw is based on the application and the thickness of the steel.
Types Of Metal To Metal Roofing Screws
- Screws that fasten the sidelap of the metal panels or attach the trim and flashing.
- Screws that attach to light gauge metal such as metal purlins.
- Screws that attach to heavy steel joists, I-beams, or steel tubes.
Trim Screws
The type of trim screw you should use depends on the panel it’s being used for and whether it’s exposed to the weather. When you have a trim screw that will be exposed to the weather, it should have a rubber sealing washer on it. If the screw isn’t in a place where it’ll be exposed to the weather, you could use a pancake head screw without a sealing washer.
An example of a screw that’s used to connect the trim to an exposed fastener panel is the ¼-14 Impax fastener. The point of the screw can penetrate 20-29 gauge trim and then attach the trim to the sheet metal.
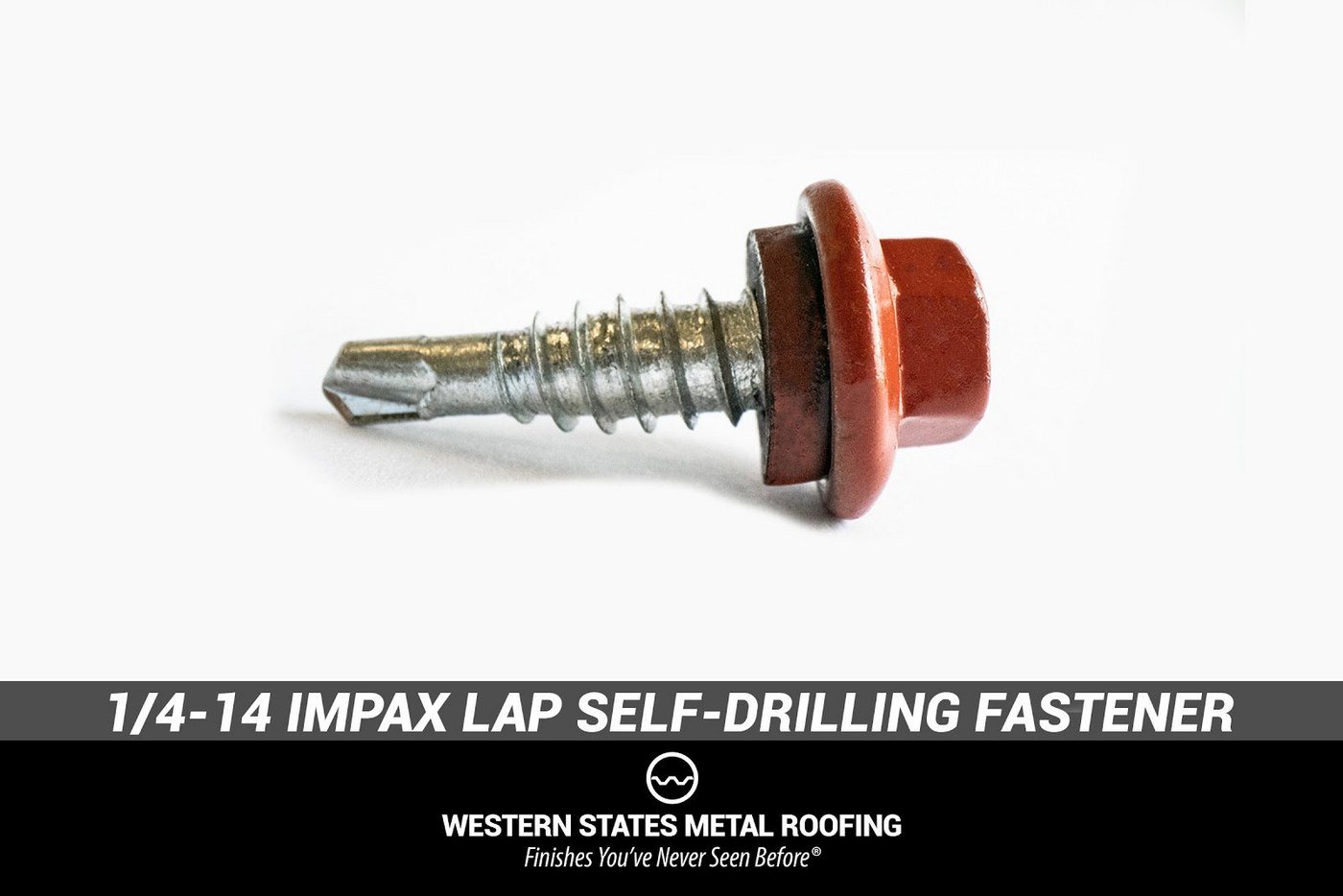
Lap Screws
Lap screws are commonly referred to as a stitch screw. The screw pattern for an exposed fastener panel will require a lap screw to attach the panel sidelap. These screws are normally placed 12” to 24” on center at the lap of the panel.

Metal To Light Gauge Metal Screws
This type of screw can be used on a metal roofing or siding job. For a metal roof, the most common application is attaching to metal purlins. For a metal siding job, it’s an attachment to metal studs.
You will use this type of screw when the thickness of the metal purlins are 14 or 16 gauge. An example of this type of screw is a #12-14 Impax.
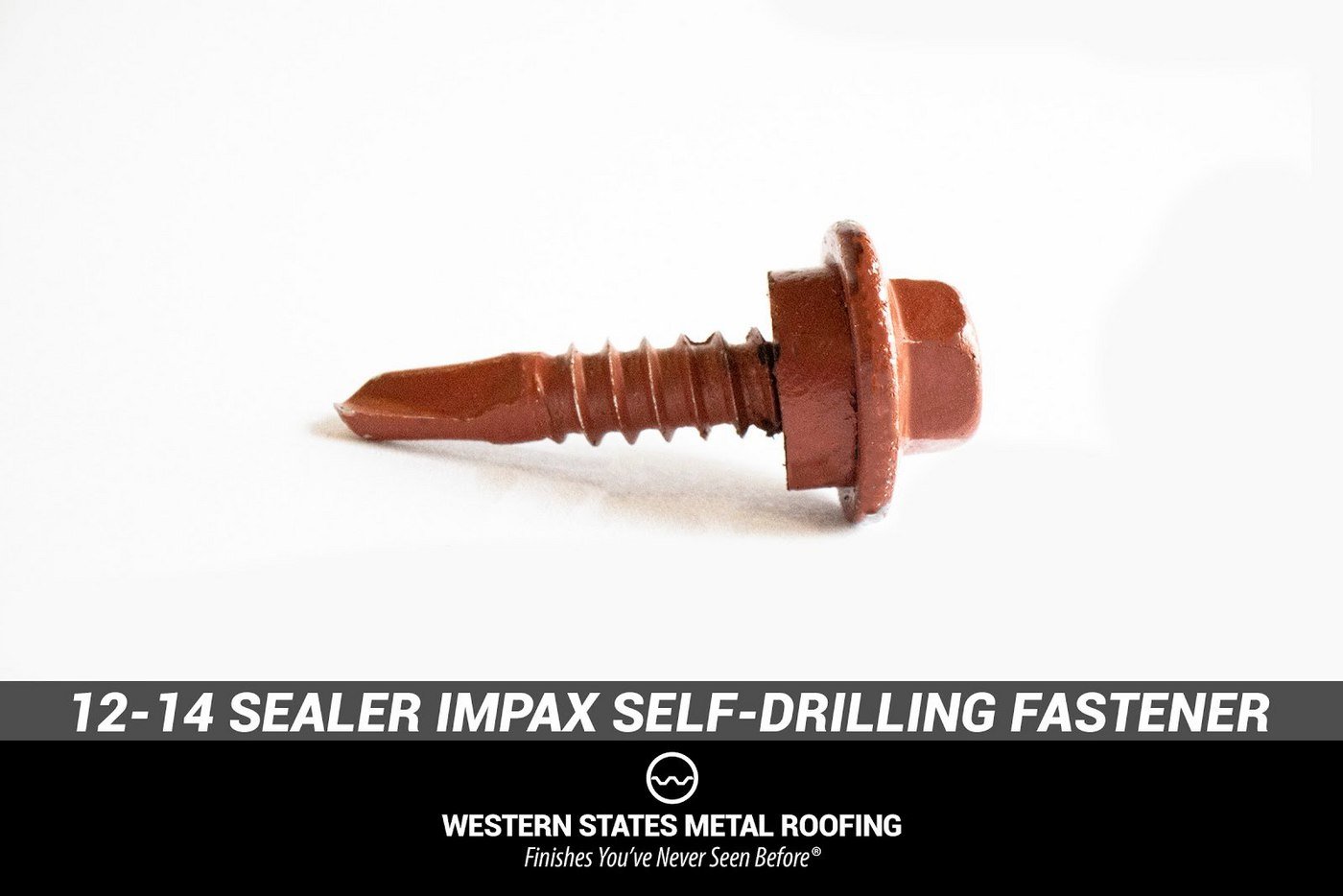
Metal To Heavy Gauge Steel Screws
This type of screw will be used when the thickness of the steel is up to ⅛” thickness or greater. As the steel gets thicker it becomes harder to fasten directly to the steel. The two most common types of screws that are used in this application are #12-24 Impax 4.5 self driller and #12-24 Impax 5 self driller.
Self-Driving/Tek Screws
Self-drilling screws are just another name for Tek screws.
Tek screws have a small carving on its tip known as a drill bit. They both drill their own hole and form mating threads. Tek screws eliminate the need to pre-drill and therefore help projects get done faster. These screws are meant for metal to metal applications only.
There is one exception, known as the reamer Tek® screw, which is designed with wings and meant to be used on wood to metal applications.
Tek screws are identified by a number from 1-5 which indicates the length of the flute, or the part of the screw which determines the level of metal thickness it can drill through. As the number gets bigger, the thickness of the metal it can go through increases.
Tek 4 vs. Tek 5 Screws
Just because a screw can penetrate heavy gauge steel, that doesn’t mean it won’t require a lot of effort. There’s only a slight difference in cost between a Tek 4 vs 4.5 vs 5. The extra time and effort that’s required when using a Tek 4 is not worth the minimal savings.
We recommend that you use a Tek 5 whenever it’s possible.
- Tek 4.5 screws can drill through .075-.375 inches of metal.
- Tek 5 screws can drill through .075-.500 inches of metal.
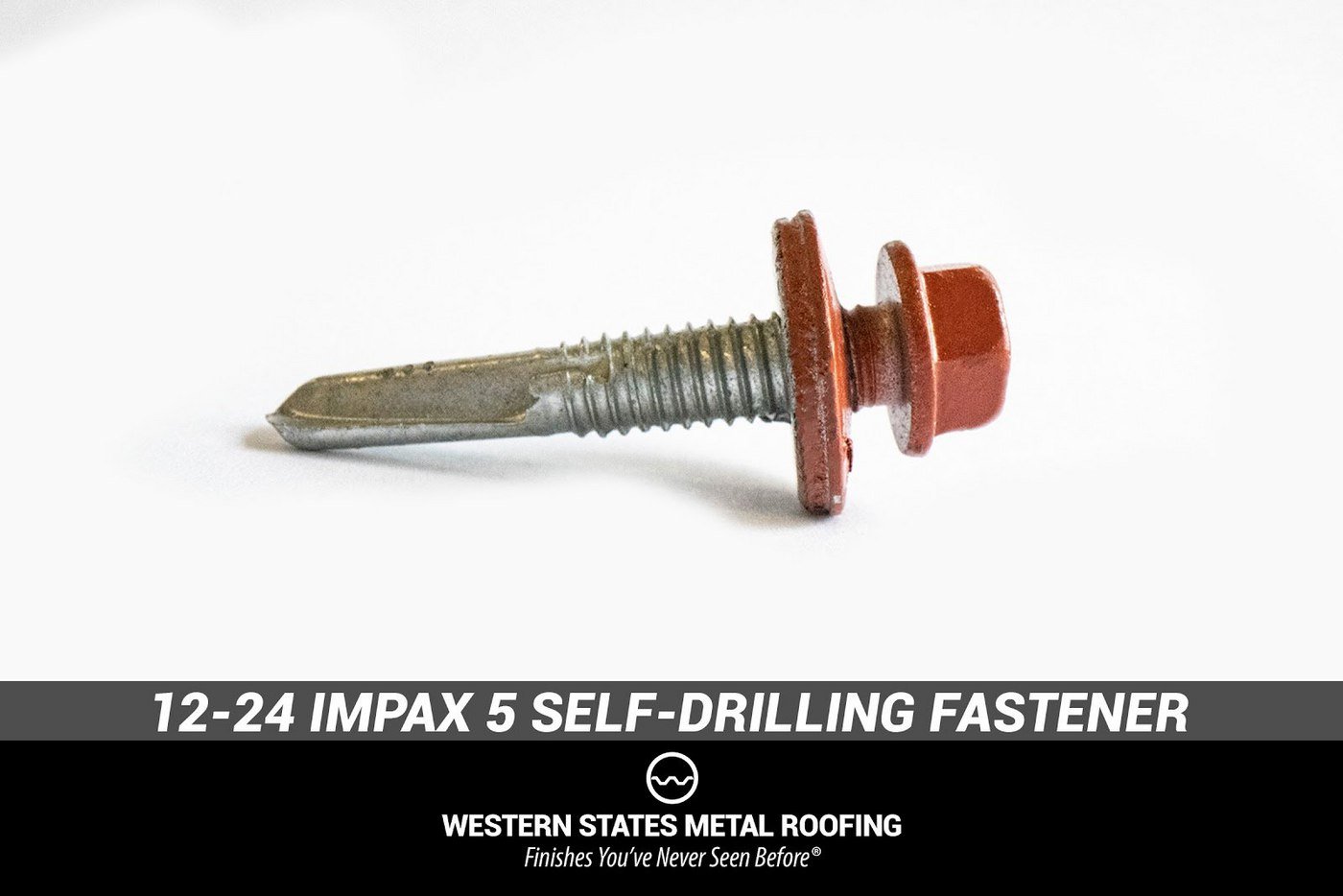
Screw Drill Points
One of the most misunderstood parts of a screw is the drill point itself. It’s common for customers to use all of these terms interchangeably. Self-drilling and self-tapping screws are often confused for being the same product.
There are several similarities between the two including both often coming in the same sizes and head types. However, they serve different purposes. If you order the wrong drill point then your screw will not function correctly.
There are three basic types of screw drill point styles and we will define each.
- Self-Drilling
- Self-Tapping
- Self-Piercing
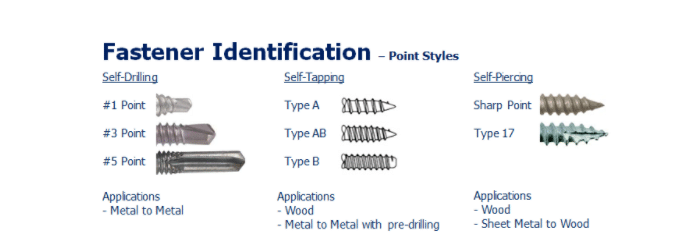
What Is A Self-Drilling Screw?
The tip of the screw will have a drill point that is capable of drilling a hole while forming the mating threads. It must be able to perform both things in a single operation. A self-drilling screw must drill its own hole to be considered self-drilling. It’s used in metal to metal applications.
What Is A Self-Tapping Screw?
This is a screw that is designed to tap threads into the material. They are not designed to drill through metal. You must pre-drill a pilot hole prior to installation. Applications are both metal and wood but are rarely used for metal roofing and siding projects.
What Is A Self-Piercing Screw?
This is a screw that is designed to both pierce a light gauge metal and also tap threads into the material. The drill point will be sharper and has two threads. You don’t need to pre-drill a pilot hole prior to installation. These are the most common type of metal to wood screws.
Choosing The Right Diameter For Your Metal Roofing Screws
The diameter of the screw is measured by the diameter of the shank. The higher the number, the wider the screw.
Choosing the correct screw will vary based upon the local building codes, climate, contractor preferences, and the engineering specifications of your job. Every job will be different and every screw has different pull-out values. The best we can do is to give you some general guidelines.
Here are the most common screw diameter sizes:
- #9 & # 10 - These are the most common sizes for metal to wood screws
- #12 - This is the most common metal to metal screw
- #14 - Wider screw that’s used in areas with heavier snow loads
Choosing The Screw Head Of Your Fastener
Fasteners come in different profiles that each accommodate different criteria.
For example, there are flat screws, also known as “pancake screws”, that are used when low profile installation is necessary. Another example are shoulder screws which feature an oversized dome beneath the head that is useful when thermal movement might distort the holes.
What Are The Different Screw Head Types?
- Hex Washer Head – The washer face provides a bearing surface for the driving sockets. These can be slotted or unslotted, although unslotted is more common.
- Pan Head – A low profile head that can be a Phillips or a square drive.
- Flat Head – This head type sinks into wood for a flush finish.
- Oval Head – Similar to a flat head, but with an oval on top for a finished look.
- Round Washer Head – Consists of a raised pan head with an integral washer formed during the heading process. The head of the screw helps prevent it from being over-driven.
- Truss Screws – Screws with a large head and low profile.
- Flat Truss Head Screws – Lowest profile head available for attaching metal to metal.
- Wafer Head – Used to attach plywood to metal.
- Drywall Bugle Head – These will fasten drywall to metal studs.
- Pan Framing – A stud-framing screw for attaching stud to track.
- Pancake Head – A very low profile head with a large bearing surface.
- Square Trim — A square drive and reduced head for tight spaces.
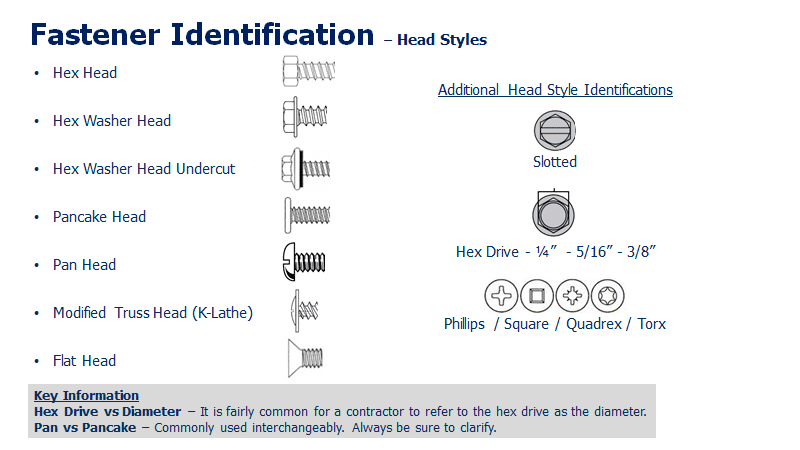
Selecting The Correct Thread Count
Thread count, also known as thread pitch or threads per inch (TPI), represents how fine the threads are on a screw. This is an important consideration because it’s part of what determines the pull out values of the screw
US fasteners refer to the thread count as threads per inch (TPI) so 24 would represent 24 threads per inch. Example: #12-24 is a #12 diameter with 24 threads per inch.
Metric fasteners refer to thread count as thread pitch, or the distance between the threads. For example, a 1.5 pitch would have 1.5 millimeters between each thread.
Smaller fasteners tend to have finer threads, so the thread count is higher.
The Importance Of Using The Correct Screws For Your Metal Panels
We covered a lot of areas in this article, but now you should have a better understanding of all the different types of fasteners available. Using the correct screws for your project is vital to the longevity of the metal roof or siding that you’re installing.
Using the wrong screws or installing them incorrectly is a simple error that can cause damage that can be easily avoided. Take the extra time to decide which fasteners work best for your project’s specifications.
Western States Metal Roofing has you covered as we offer all the accessories you’ll need for a successful metal panel installation. We carry a wide variety of fasteners to choose from when you order your metal roofing or siding panels.
For more information on fastener installation, we recommend reading:
How To Install A Metal Roof With Fastening Screws [Stop Metal Roof Leaks]
How Many Screws Do I Need For Metal Roofing? Screw Pattern & Placement Best Practices